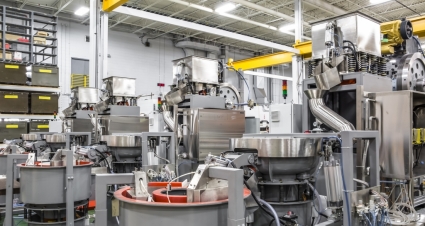
The Waterbury Farrel Vibro-Cleaning & Polishing machine consists of two vibrating bowls. In the first bowl, cases or bullets are degreased, pickled and passivated using three separate solutions in sequence. The parts are then transferred to the second bowl, where they are dried and vibrated in a polishing media. Parts are cycled in batches weighing 45 kg (100 lbs).

The Waterbury Farrel Wash, Rinse, Lube & Dry Machine removes coolant and contaminants from formed parts. A long, rotating drum carries parts through a series of liquid baths. Parts are degreased with an alkaline solution and water rinse, then lubricated with a soap solution and dried with hot air.
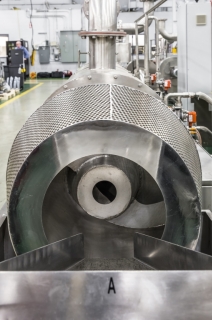
The Waterbury Farrel Pickle, Rinse and Dry Machine removes copper oxide and dust from brass parts after annealing. A long, rotating drum carries parts through a series of liquid baths. Copper oxide is removed with sulphuric acid solution and water rinse. The parts are lubricated with a soap solution, then dried with hot air.
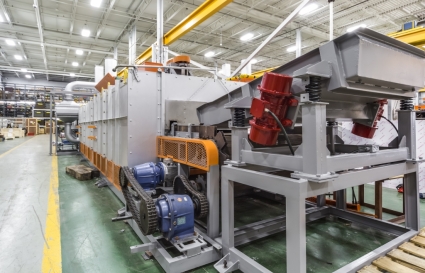
The Waterbury Farrel Annealing Furnaces are used to anneal brass parts after forming. The annealing furnace is an electrical resistance heating furnace either with a continuous metal mesh conveyor belt or a fabricated long drum with an internal screw type auger, with automatic temperature control system. Parts are deposited directly onto the conveyor or at the opening chute of the drum, where they travel into the multi-zone electric furnace with an option of a nitrogen atmosphere at a specific speed. It also has a cooling zone at the end to cool the parts to a reasonable handling temperature before offloading.
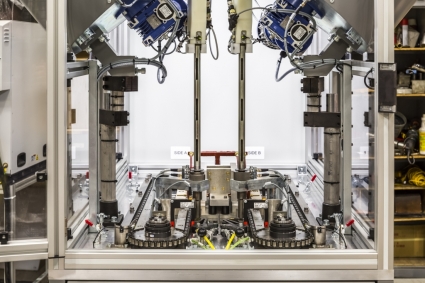
The Waterbury Farrel Body/Mouth Annealing Machine anneals only the specific body area or neck and mouth of the pre-formed or fully-formed rifle cases. Cases/case components are fed into the machine, and carried single-file through induction heaters, where the water-cooled generator provides the excitation for the induction coils. The machine provides individual rotary motion to each case while passing through the linear feeding system of the annealer. Finally, air-cooled cases/case components are ejected.
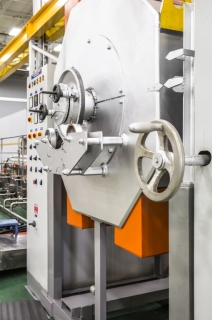
The Waterbury Farrel Hardening Furnace is used to harden steel cores after they emerge from the Steel Core Swager. Steel is hardened when heat soaked at 900°C (1652°F) for 60 minutes then quenched in water. The steel solidifies into a martensite stage (brittle and almost crystalline steel). The rotating furnace retort handles batches weighing up to 35 kg (77 lbs). The furnace includes a quench tank with outfeed conveyor.