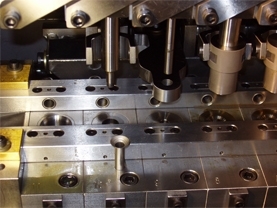
The Waterbury Farrel Die Set Press provides high operating speeds, positive part control and rapid tooling changeover. All of the components necessary for part forming and timing are included in the system; only simple tooling is required for each die set. Each part is handled under full time positive control of the transfer or tooling, preventing tool or machine damage.
The DS Press operates up to 3 times faster than transfer die presses producing comparable parts. Unlike complex transfer dies in traditional straight side presses, the DS Series employs simple, low-cost die sets; eliminating the complication and long lead times associated with transfer die sets.
Low development lead times, faster operating speed and greater cost efficiency make the Waterbury Farrel DS Press the clear choice in maximizing ROI.
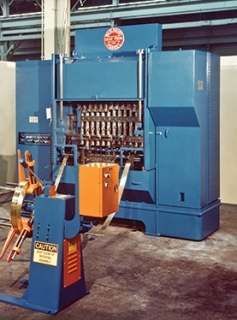
The Individual CAM-Operated Plunger (ICOP) Press is a universal die set press with low-cost tooling systems: simple punches, die inserts, stripper sleeves and transfer fingers. Independent stations permit easy tooling changeover with reduced downtime. These improvements as well as the elimination of carrier strips and multi-row blanking realize significant yield savings. The versatile Waterbury Farrel ICOP Press will perform the function of several lesser single function machines, allowing minimization of capital and labor costs.
Waterbury Farrel ICOP presses are built in five standard frame sizes depending on the required number of stations, and a High Tonnage (HT) Press is available as an option.
Each ICOP Press integrates up to 14 different forming operations. These include blanking, cupping, drawing, step drawing, wiping, drifting, fluting, ironing, reverse drawing, bulging, curling, necking, body flanging, bottom piercing, stamping or embossing, threading, beading, knurling, side-lettering, bumping, side piercing, top flange piercing, trimming and many more.
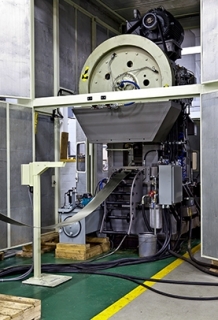
The Waterbury Farrel Double Action Blank and Cup Press is ideally suited for high volume cup production in downstream metal forming processes.
The action of the Press is purely mechanical with no pneumatic or hydraulic pads required, ensuring complete working efficiency with no loss of tonnage. Waterbury Farrel Blank and Cup Presses are available in five sizes with a series of customizations available, including a double crank design for heavier material and reduced holding pressure.
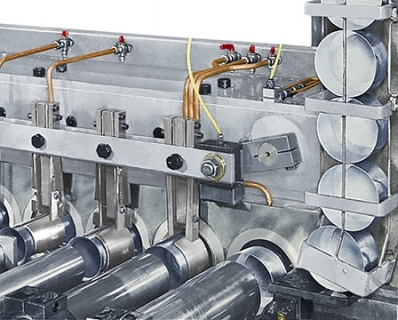
Designed for forming applications requiring a significant draw depth, the Waterbury Farrel Horizontal Redraw is characterized by its small footprint and rapid redraw with no interim annealing.
Capable of drawing clipped shells up to 9" long using cups of up to 6" in diameter, no other press delivers a length to diameter ratio of 12:1 at a rate of up to 220 parts per minute. The Horizontal Redraw press is capable of producing shallow and deep draw, tapered wall and reduced sidewall containers.